Every since getting one of the v4 models back in late 2018, the Salsa Warbird has been one of my absolute favorite bikes. I’ve ridden on all surfaces, and it’s been great, with only one recurring problem: front shifting.
These days bikes ridden anywhere but pavement are almost exclusively rear-shifting-only (1x) — without a front derailleur — and for good reason. Unfortunately, when I bought my Warbird there weren’t many (any?) 1x groups for drop bar use; Shimano hadn’t even announced their excellent gravel-focused GRX group. So, my bike came with the best bang-for-the-buck drivetrain at the time, Shimano 105 R7000. This remains an excellent groupset, and I put it on my new road bike, but a couple things about it were a bit lacking for off-pavement use: lack of a clutch derailleur to keep the chain taut when things got rough, and the front derailleur.
Early on I switched the rear derailleur to a clutched Ultegra RX (RD-RX800-GS), which was basically a preview of GRX, and worked wonderfully. It dropped right in place on the bike and Just Worked to solve chain slap. But, I still had one more problem… The front derailleur.
Located where the rear wheel flings debris, front derailleurs are quite prone to getting gunked up while riding, and (unfortunately) the Warbird exacerbates this by having the shift cable exit the frame at the bottom bracket, behind the seat tube, facing upward. This location collects whatever flings off the tire and is a very hard place to seal a moving cable. Coupled with our gritty, chloride-treated dirt roads, the result has been shift cables and housing corroding and binding far before any other drivetrain parts wear.
This corrosion leads to extra drag on the shift cable needed to shift, up until things bind firmly, after which the sacrificial Main Lever Support L (part number Y63X80010) in the shifter to breaks (exploded view). The overall design of this sacrificial part is great; a removable and cheap plastic bushing on the shift/brake lever blade that presses against the metal piece that handles the shifting. If the cable becomes too tight this $3 piece fails before anything else in the shifter, and replacing it takes seconds. But, the cable and housing also need to be fixed, and COVID-era parts shortages (these supports were unobtainium for about 12 months — I was using 3D printed ones for a while) and it all quickly becomes an irritation.
I’d lived with front shifting quirks for a couple years as most of the time it was fine, but losing the front derailleur was always in the back of my mind. Mountain bikes have this way for years, with a rear cassette that provides all the range needed, and this has become common on new gravel bikes.
After front shifting failed early on in De Ronde van Grampian and I ended up stuck in the big ring, I realized two things: I should get rid of the front derailleur, and I don’t need quite all the range that a 50-34/11-34 2×11 drivetrain offers. I use most of the range, but could lose a little on the top and bottom end of the range and be fine.
The first change was to remove the front derailleur, which was made easy by the front shift housing being split with a barrel adjuster below the handlebar. I was able to pull the cable and remove the housing all the way back to just under the the bar, leaving 2″ stub of housing unobtrusively peeking out of the bar tape. Next time I rewrap the bars I’ll remove this, but for now it’s fine.
Then to finish the conversion I fitted a Wolf Tooth 42t chainring specifically designed with an offset designed for 1x. None of the single-ring chainring bolts that I had around the house fit right, so I grabbed some of Wolftooth’s matching chainring bolts and it was all set. The ring fits the crank perfectly, worked great with the original chain length, and the I could shift across the whole of the cassette without any rear adjustment.
I did two rides on local rolling dirt roads and except for some longer steep climbs things were good. I was feeling good for both rides, so I didn’t mind having to grind out the longer climbs in sub-optimal cadence, but I realized I might need some more range on longer days. I’d also been concerned the left brifter would be flappy and noisy without a shift cable connected, but it’s just the same as before.
Next up was getting more gear range…
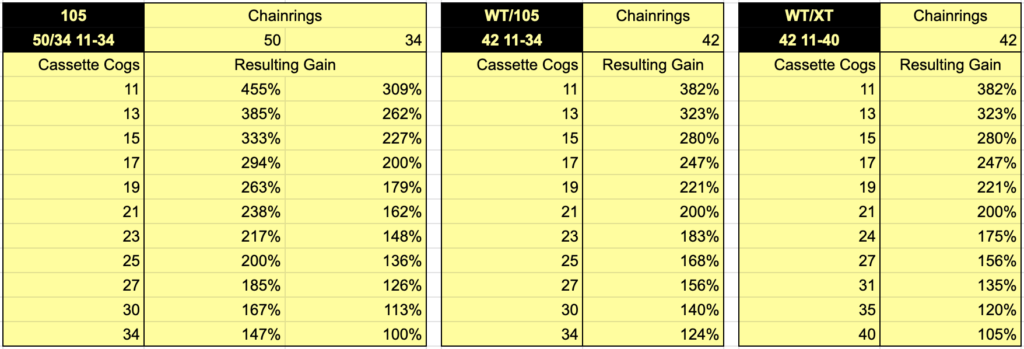
The original Shimano 105 R7000 drivetrain, with 50/34 chainrings and an 11-34 cassette, gave a range from 455% to 100%, plenty for all my riding, but with a whole bunch of overlap. While I’d use the lowest ratio gears somewhat frequently, I’d almost never use the highest gear because at typical cadence I’d be moving well above 33 MPH. At those speeds I’m probably coasting down a hill and no longer pedaling.
After changing to a single 42t chainring the available ratios were 382% to 124%. At the high end this is nearly identical to everything but the rarely-used smallest cog, but at the low end it was like I lost the easiest two gears. On a couple test local couple-hour rides I didn’t absolutely need them, but it did require a bit more effort on some of the harder climbs.
With 11-speed mountain bike drivetrains on the decline, I came across Shimano XT 11-40 cassettes on sale and decided to try a bigger cassette on the rear of the bike. I was still on the original cassette and it was nearly worn out, so a change was due. This required a 1.85mm spacer to make the MTB cassette fit on a road freehub, which moved the cogs outboard, but a few limit adjustments and all was good. Now with a range of 382% to 105% it was almost identical to what I’d use on the original 2x setup.
The larger cassette fit pretty well, but caused some small quirks in spacing with the upper jockey wheel: the B-tension screw had to be cranked in almost all the way to have the gap set properly on biggest cog. It was quite a fiddly adjustment, as a quarter turn too far one way would have the jockey wheel rubbing on the cassette and a quarter turn the other would make shifting slow. This much B-tension also unwrapped the chain from the cassette a fair bit, making me concerned that with less chain on the cassette while pedaling the chain and cassette would wear faster than normal.
At this point I did a test ride and everything worked great when riding. Between the new chain (old was at 0.5%), cassette, and chainring the drivetrain was silent and I didn’t have a bit of trouble, but I still wanted it to be better.
A few days earlier I’d ordered a Wolftooth RoadLink DM, a nifty part that replaces a link in rear derailleurs like mine, repositioning it to handle larger cassettes. This is advertised to improve chainwrap and shifting performance, and immediately after installation the benefits were apparent. On the biggest cog chainwrap is much better, the derailleur no longer looks over-extended, the B-screw doesn’t need to be turned all the way in, and shifting feels more spot on.
While I could have fitted a Shimano GRX RD-RX812 derailleur instead of using the RoadLink DM on the Ultegra RX, this would have cost $90 more than the RoadLink DM, and I’m not sure it’d be any better.
All done, total cost for this was $265.03 after tax, and with a new cassette, chain, and chainring, I’ve now basically got a new drivetrain.
Wolf Tooth Chainring: $84.95
Wolf Tooth Chainring Bolts: $26.45
Shimano XT Cassette: $95.39
Shimano SLX/105 Chain: $26.49
Wolf Tooth RoadLink DM: $31.75
I’m quite happy with how this all turned out. A problem is solved, worn out things were upgraded, functional parts were kept, and it works great. My Warbird is ready for another year of gravel fun.
Comments closed